Renault's Spanish factories, undercover and pioneers in AI
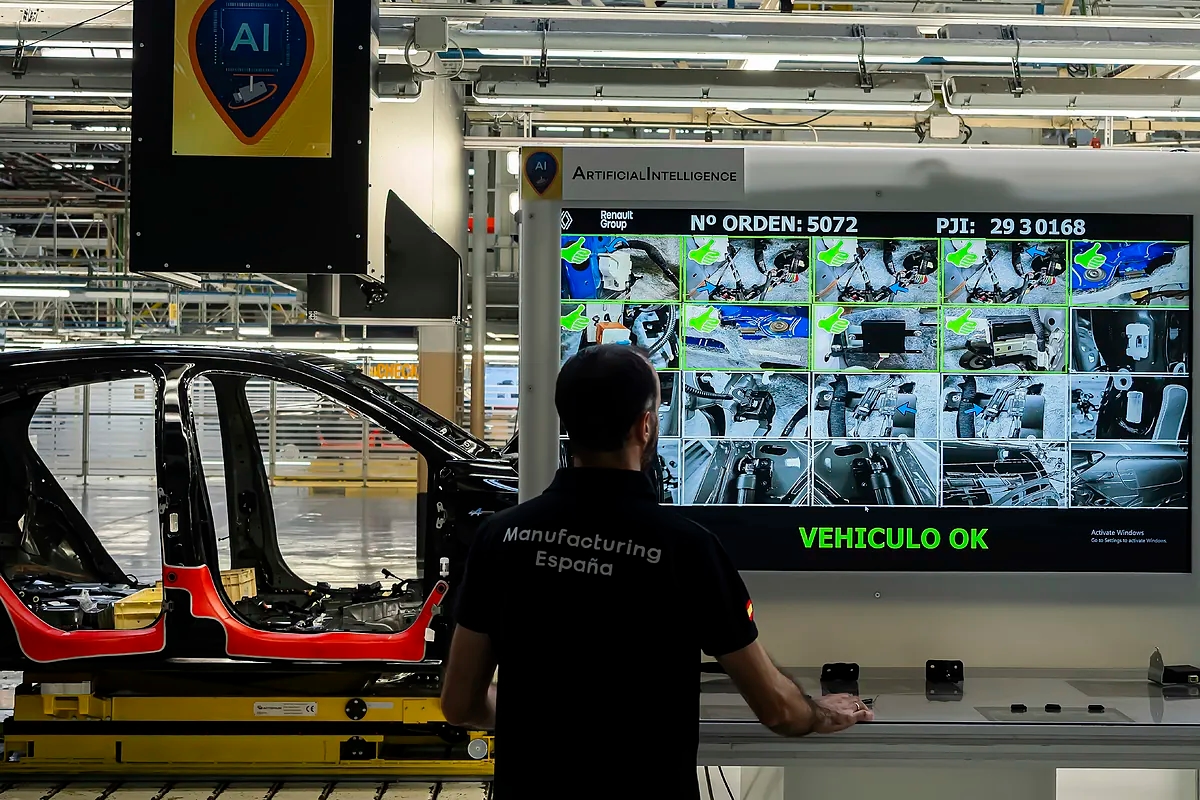
Renault doesn't plan to move any of its Spanish-made models to France , but it may house some electric models for the C or D segments, according to Thierry Charvet, the French group's Director of Industry and Quality. "Our current strategy is to develop the electric ecosystem in France, but if we want all our vehicles to be electric in 10 years, we will have to, to some extent, manufacture them elsewhere," he said.
What's more, he didn't rule out the possibility of Spanish factories assembling some Dacias in the future. "With their high degree of automation and ability to contain costs, they could become more competitive than other locations where we manufacture Dacias. But we don't need more capacity today. When the time comes, we'll consider it."

Charvet made these statements during a visit to support Renault Group's Industrial 2.0 strategy, with a particular focus on Plant Connect, a project led in Spain and based on Artificial Intelligence (AI).
Currently, Valladolid and Palencia assemble the Captur, Symbioz, Rafale, Espace, and Austral, as well as two Mitsubishis. In 2024, they were responsible for 14.5% of the company's global production and 50% of its hybrids. In total, 210,000 cars are produced in Valladolid and 139,000 in Palencia. In addition, the parts manufactured at the Valladolid Bodywork plant, such as 728,178 bumpers and 204,039 batteries, are also produced.

"In an environment changing at an unprecedented speed, AI has reached every corner of our plants and allows us to manage two million data points per minute to be more efficient, faster, and competitive. These initiatives are then exported to all of the group's factories," explains José Martín Vega, director of the Iberia Vehicle Industrial Park.
In this regard, the manufacturer launched a four-year plan in 2023 to optimize production costs, shorten vehicle development times, save energy in production, and improve construction times. Halfway through, they have already achieved more than half of their goals.

For example, the new Renault Twingo, due to arrive in 2026, has 25% fewer parts than the Mégane, and its development time has been reduced to two years, compared to three or four for previous models. And fuel efficiency has improved by 26% from 2021 to 2024.
This substantial progress puts them on track to achieve the industry's goal: a 40% reduction by 2027. And the more than 50% drop in emissions from its plants between 2019 and 2025 helped rank Renault Group among the top manufacturers in energy consumption and CO2 emissions per car produced. To achieve this, they developed their own energy management system, which includes 10,000 energy meters and sensors as part of their digital transformation.

According to Charvet, the Reindustria 2027 plan "has placed digitalization and AI at the heart of our operations. Thanks to the industrial metaverse, we can monitor all operations, including the most basic ones, in real time, around the world. This digital twin makes it easier for us to respond immediately when any discrepancy occurs, optimize maintenance, improve quality, and streamline decision-making."
Spain, pioneerSpecifically, the Connect Plan was launched in Palencia, although it is already being implemented worldwide. It allows for detailed monitoring of operational and commercial indicators, facilitating real-time problem identification and resolution. In the event of a deviation, action plans are proposed based on data stored in Google Cloud, allowing for faster and end-to-end activity control. Likewise, an advanced system performs geometric vehicle control to automatically validate manufacturing processes with exceptional precision and reliability. In addition to operational alerts, predictive actions are developed, for example, regarding gas consumption the following day.

The project offers a comprehensive overview of several stages: orders; suppliers; inbound (parts logistics to the factory); production (stamping, plating, painting, and assembly); CLE (delivery logistics center); and outbound (vehicle logistics to customers).
elmundo