Technology revolution at BMW: This is what makes the New Class so special
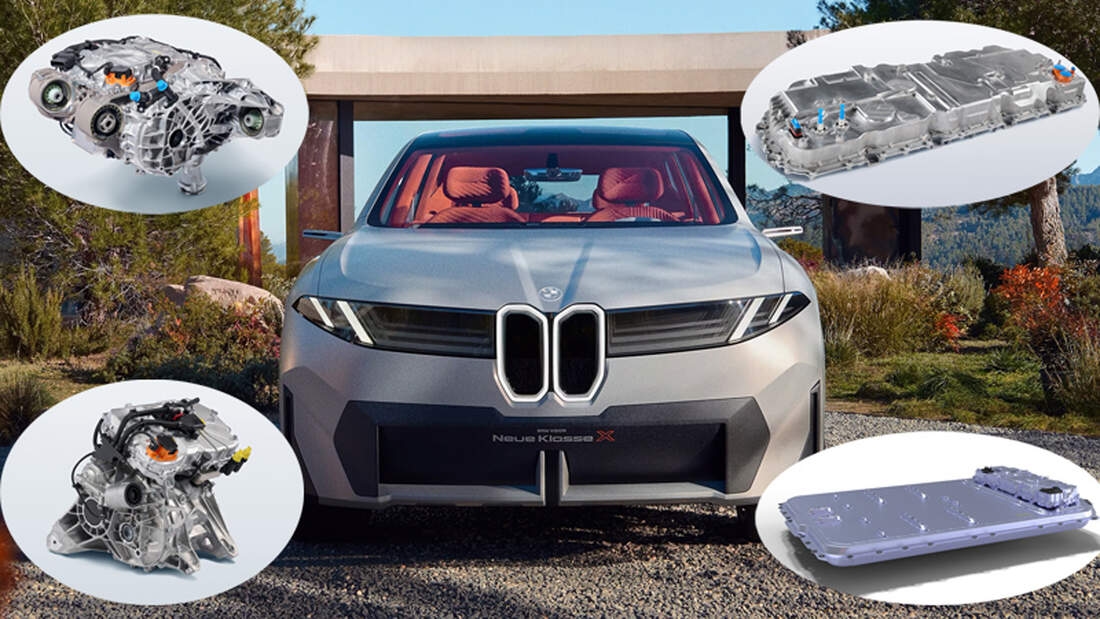
It is the largest investment in BMW's history and at the same time a bet on the future of the automobile. BMW is investing several billion euros in the development and production of the new platform, on which up to eight models are to be released by 2027. The first is the iX3 successor, which will be presented in autumn 2025. BMW has numerous innovations in the development of the New Class in order to ensure that the brand can compete globally. We describe the most important features below.
Instead of the previous box-shaped battery cells (prismatic cells), BMW is using new round cells (cylindrical cells). These can be imagined in a simplified form like standard flashlight batteries. BMW developed the cell chemistry itself and defined its production conditions in a pilot factory. In principle, the Bavarians would therefore have no problem producing their own self-developed power storage units themselves. However, mass production will come from suppliers (e.g. CATL). The reason for this is economic aspects, because building their own battery "gigafactories" would be too expensive given the number of units BMW produces.
BMW will use a new system for the drive batteries in the New Class. The cells will be inserted individually into the battery housing instead of being bundled into packages as before. At the same time, the high-voltage battery will no longer be an additional component that is attached under a body. Instead, the drive battery will be a body component and practically forms the underbody of the respective vehicle. The advantage of this technology: In addition to the reduction in weight and volume compared to the previous batteries of the electric BMW, this design is cheaper in vehicle production, and the new batteries are so flat that they can be used in everything from sports cars to SUVs without compromise.
However, there is also a major disadvantage compared to the previous design. If individual battery cells have to be replaced during the life cycle of the car, this would mean a much higher installation effort than with an externally mounted traction battery.
For the first time, BMW is integrating the 800-volt technology already offered by some other manufacturers. Compared to the 400-volt system previously used, this increase in voltage brings a number of advantages. The most important for the customer is drastically reduced charging times at fast charging stations; BMW itself states that the New Class can recharge up to 300 km WLTP range within 10 minutes. Another advantage of the 800-volt charging technology is lower charging losses, which contributes to the overall efficiency of the vehicle. For the manufacturer, the fundamentally more expensive 800-volt technology also has economic advantages, especially because of the less expensive wiring in the car.
BMW is particularly proud of the "Energy Master". This is a system housed in a closed housing. The BMW Energy Master is placed directly on the high-voltage battery and takes over the central control of the energy flows. It connects the high and low-voltage power supply and ensures smooth data transmission within the battery system. It also regulates the energy distribution to the electric motor and the on-board network. The BMW Energy Master is not a classic power electronics system, but a highly integrated control and communication center for the high-voltage battery. While the power electronics are primarily responsible for converting and regulating the electrical energy between the battery and the electric motor, the Energy Master takes on a higher-level function. BMW developed this control module itself and also builds it itself. Production for BMW's global electric car production takes place at the BMW plant in Landshut.
A brand that has "engines" in its name is of course particularly challenged in this regard. BMW is relying on an expanded engine strategy in the sixth generation of eDrive technology (Gen6). In addition to the well-known synchronous motor (SSM), an asynchronous motor (ASM) is also being used for the first time. The ASM technology, which is used on the front axle of the BMW xDrive variants of the New Class, uses induction to generate the rotor's magnetic field. The rotor of the ASM consists of a metal cage, which has advantages in terms of size and production costs.
Parallel to the introduction of ASM technology, the existing SSM drive unit was extensively developed further. The rotor, stator and inverter components were adapted to the new 800-volt architecture, which brings fuel consumption benefits and increased performance. The revised oil and water cooling as well as a lighter and stiffer motor housing bring further progress. The spur gear integrated in the motor housing has also been improved; it now runs more quietly and with less friction.
The inverter, the central control element of the electric motor, uses modern silicon carbide semiconductors (SiC) and is fully integrated into the motor housing. It converts direct current from the high-voltage battery into alternating current for the electric motor. This is also an in-house development by BMW.
BMW has not yet given precise performance data for the two electric motors. The rear synchronous motor will have a power range of 200 to 300 kW (272 to 408 hp), the front asynchronous motor should be able to deliver at least 120 kW (163 hp). In a combination of several motors, the 800 kW mark (1,088 hp) should be within sight, which promises absolutely insane performance. We have already been able to gather initial impressions of this with a prototype .
auto-motor-und-sport