Batteries, from mines to roads: the path of materials
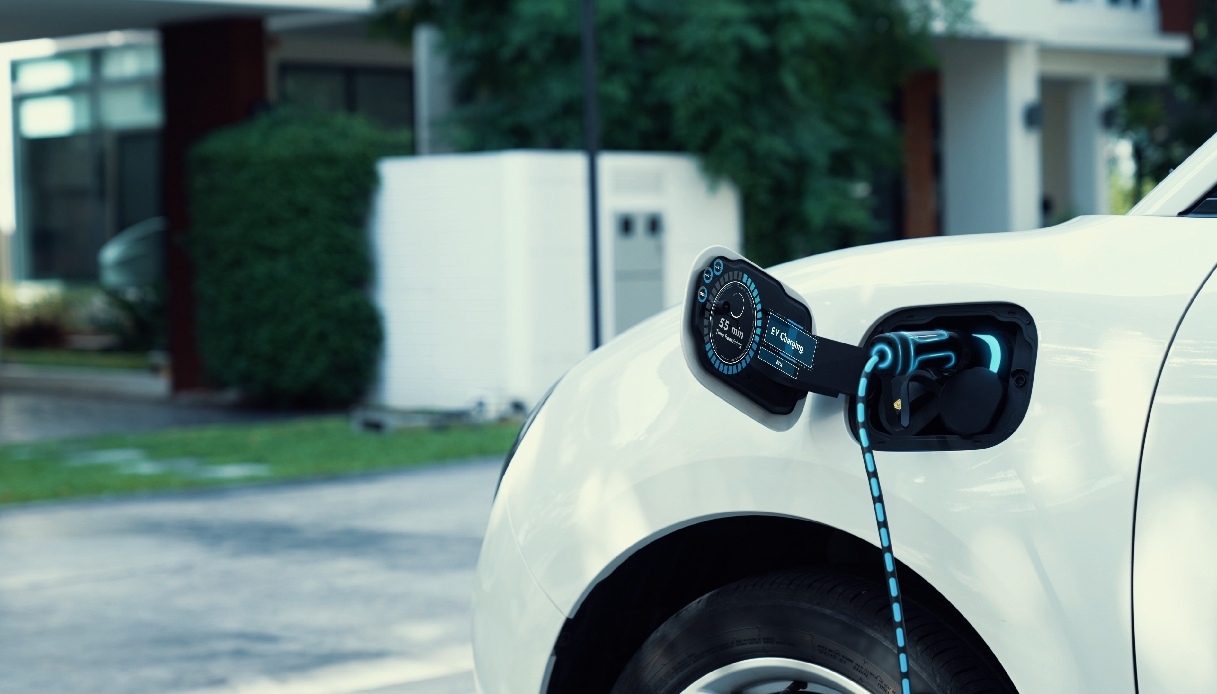
At the heart of the energy transition, electric car batteries are the linchpin of a silent but powerful revolution. Behind every zero-emission vehicle lies a complex and fascinating journey, which begins in the depths of the Earth and culminates on the streets of our cities. Lithium, cobalt, nickel, graphite: elements extracted in remote corners of the planet, often in critical environmental and social conditions, are transformed into sophisticated energy accumulators.
These materials, once assembled, power sustainable mobility, but their lifecycle raises crucial questions about sustainability, human rights, and geopolitics. Exploring the journey of these materials, from mines to roads, is to understand the challenges and opportunities of an increasingly electric future.
The basic raw materials: characteristics and requirementsElectric car batteries are mainly based on lithium-ion (Li-ion) technology, which offers a good compromise between energy density, power and durability. The basic raw materials that compose them are:
- cathode: The positive electrode contains lithium combined with transition metals such as nickel, manganese, cobalt, aluminum, or iron. Lithium is essential for transporting the ions that generate current, while transition metals directly influence the battery's energy density, power, and stability. For example, NMC (nickel-manganese-cobalt) and NCA (nickel-cobalt-aluminum) chemistries offer high energy density, while LFP (lithium-iron-phosphate) stands out for safety and durability. Key requirements for cathode materials include high purity, chemical and electrochemical stability, and good ionic and electronic conductivity;
- anode: the negative electrode is typically made of graphite, a low-cost material with good conductivity and the ability to store lithium ions. Silicon is being explored as a potential substitute to increase capacity, although it presents challenges related to volumetric expansion. Lithium titanate (LTO) offers greater safety and durability, but with lower energy density. The main requirements for anode materials are high specific capacity, low working voltage, good conductivity and stability during charge/discharge cycles;
- electrolyte: acts as a conductive medium for lithium ions between cathode and anode. It is usually composed of lithium salts dissolved in organic solvents, which must ensure high ionic conductivity, stability and safety (low flammability). Research is also focused on solid electrolytes as a safer alternative;
- separator: it is a porous membrane that prevents physical contact between the electrodes but allows the passage of lithium ions. It must have high mechanical resistance and thermal stability to ensure the safety of the battery.
The journey of the essential raw materials for electric car batteries begins with extraction from natural deposits. Lithium, cobalt, nickel, manganese and graphite are recovered through various mining techniques. Lithium can be extracted from brine deposits via solar evaporation or from rock minerals by chemical processes. Cobalt, often extracted as a by-product of nickel and copper, raises serious ethical questions, especially in artisanal mining. Nickel and manganese are obtained from various types of deposits, while graphite can be mined or produced synthetically.
This phase of extraction is marked by significant critical issues . High water consumption, ecosystem disruption, high energy costs and waste management are common issues. For cobalt, working conditions and child labor are serious ethical concerns. Furthermore, the geographic concentration of some resources creates geopolitical dependencies.
The raw minerals are then subjected to refining , a set of industrial processes aimed at obtaining the pure metals or chemical compounds needed for battery production. Lithium is refined through chemical processes to obtain pure salts. Cobalt, nickel and manganese require complex metallurgical and chemical purification operations. Natural graphite is purified, while synthetic graphite is produced through heat treatments. The criticality of refining lies in the intense consumption of energy, the production of potentially polluting waste and effluents and the use of dangerous chemicals.
The design of the cellThe design of electric car battery cells is a constantly evolving field, closely linked to the chemistry of the materials used and to the progress in technological evolution . The choice of materials for the cathode (such as NMC, NCA, LFP), anode (mainly graphite, with studies on silicon), electrolyte (from liquids to safer solid electrolytes) and separator directly influences the performance of the battery in terms of energy density, power, safety and duration. Research is focused on the discovery of more performing, economical and sustainable materials, such as alternatives to cobalt and solid electrolytes.
In parallel, cell design plays a fundamental role. Different configurations have evolved, from cylindrical cells (with standardized formats that are continuously being optimized) to prismatic cells (for better packaging), pouch (lightweight and flexible) and blade (which offer a good structural compromise). The evolution of the design aims to maximize energy and power density, improve thermal management and the overall safety of the battery pack.
Finally, manufacturing processes are a crucial aspect, with the aim of reducing costs, increasing production speed and ensuring high and uniform cell quality through automation and advanced technologies. The synergistic interaction between material chemistry, cell design and manufacturing processes is essential for the development of increasingly efficient, safe, economical and sustainable batteries, crucial for the advancement of electric mobility.
From cell to battery packThe process that transforms individual electrochemical cells into the complex battery pack of an electric car is a highly engineered and sophisticated assembly operation. The primary goal is to convert the capabilities of individual cells into a safe, efficient and reliable energy storage system capable of powering the entire vehicle.
Battery pack engineering involves several crucial areas. Initially, cells are grouped into modules , whose configuration (series and parallel) determines the voltage and capacity. Optimizing the number of cells per module is critical, considering energy density, thermal management, and safety. Thermal management is vital to controlling the heat generated during operation, using air or liquid cooling systems and temperature sensors.
The Battery Management System (BMS) is the brain of the battery that monitors voltage, current, temperature, balances the charge between cells, estimates the state of charge and health, and provides crucial protections against overcharging and overheating, while also communicating with the vehicle. Safety is a priority, with mechanical protections, prevention of thermal propagation and emergency disconnect mechanisms. The structural integration of the pack into the vehicle chassis is designed for robustness and mass distribution, while high-voltage electrical connectivity must ensure efficient and safe current flow.
Battery pack assembly is an automated industrial process that begins with cell selection and testing. These are then assembled into modules, with reliable electrical connections and integration of thermal management systems and sensors. The BMS is then installed and the modules are placed in a protective casing. The assembled pack is subjected to rigorous functional and safety tests before sealing and finishing. Automation is essential for precision and high productivity, ensuring the quality and long-term reliability of the energy heart of the electric vehicle. In short, battery pack creation is a multidisciplinary process that merges electronics, thermodynamics, mechanics and chemistry to create a high-performance and safe energy storage system.
Virgilio Motori